End-to-End Integration: Bridging Research and Production in Materials Science
The convergence of research and production in materials science through end-to-end integration is instrumental in achieving innovation, efficiency, and quality-driven manufacturing. The philosophy of end-to-end integration echoes the principles of synergy, where the sum of a system is greater than its individual parts. In the realm of materials data management and materials informatics, MaterialsZone's platform presents a quintessential example of this seamless integration.
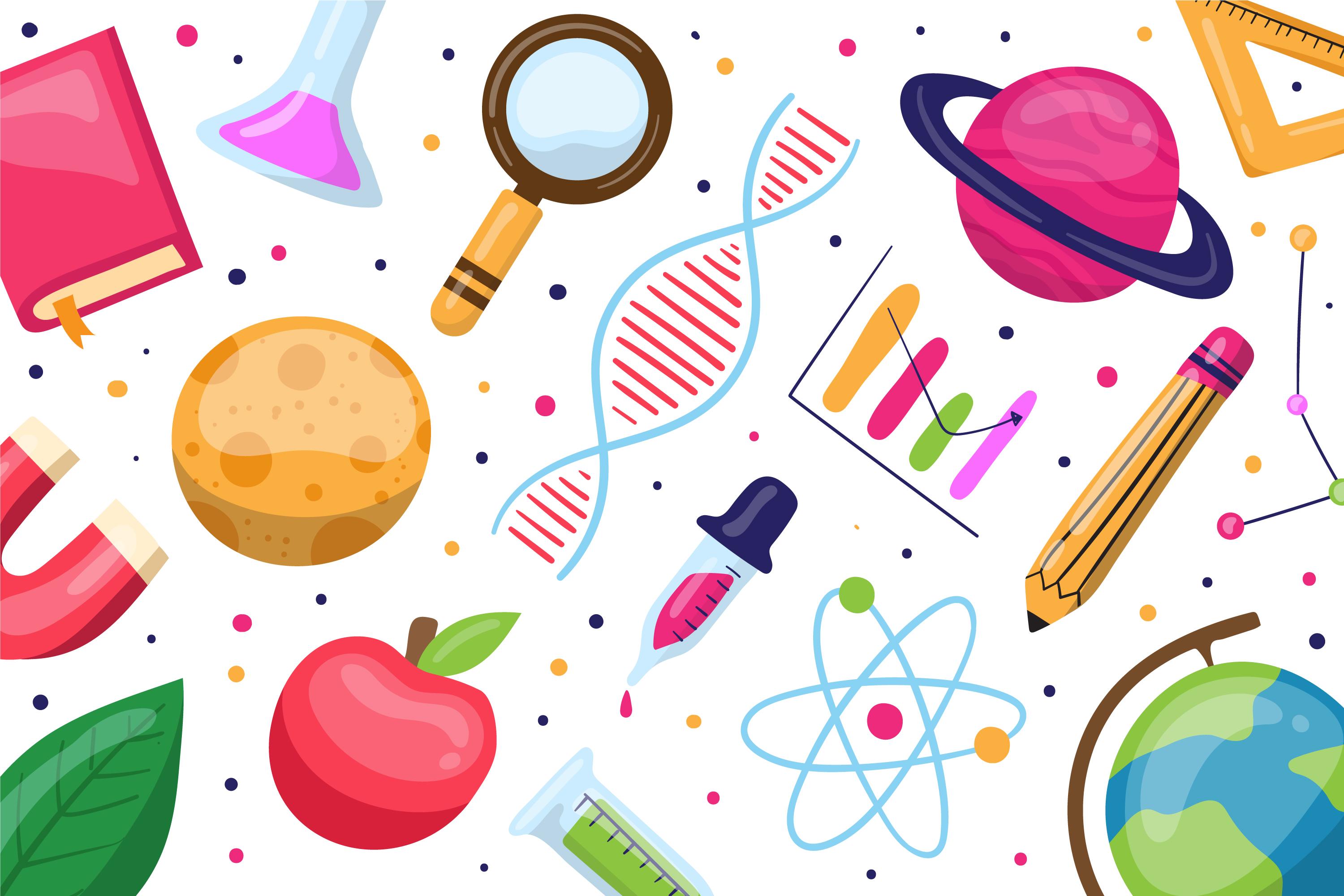
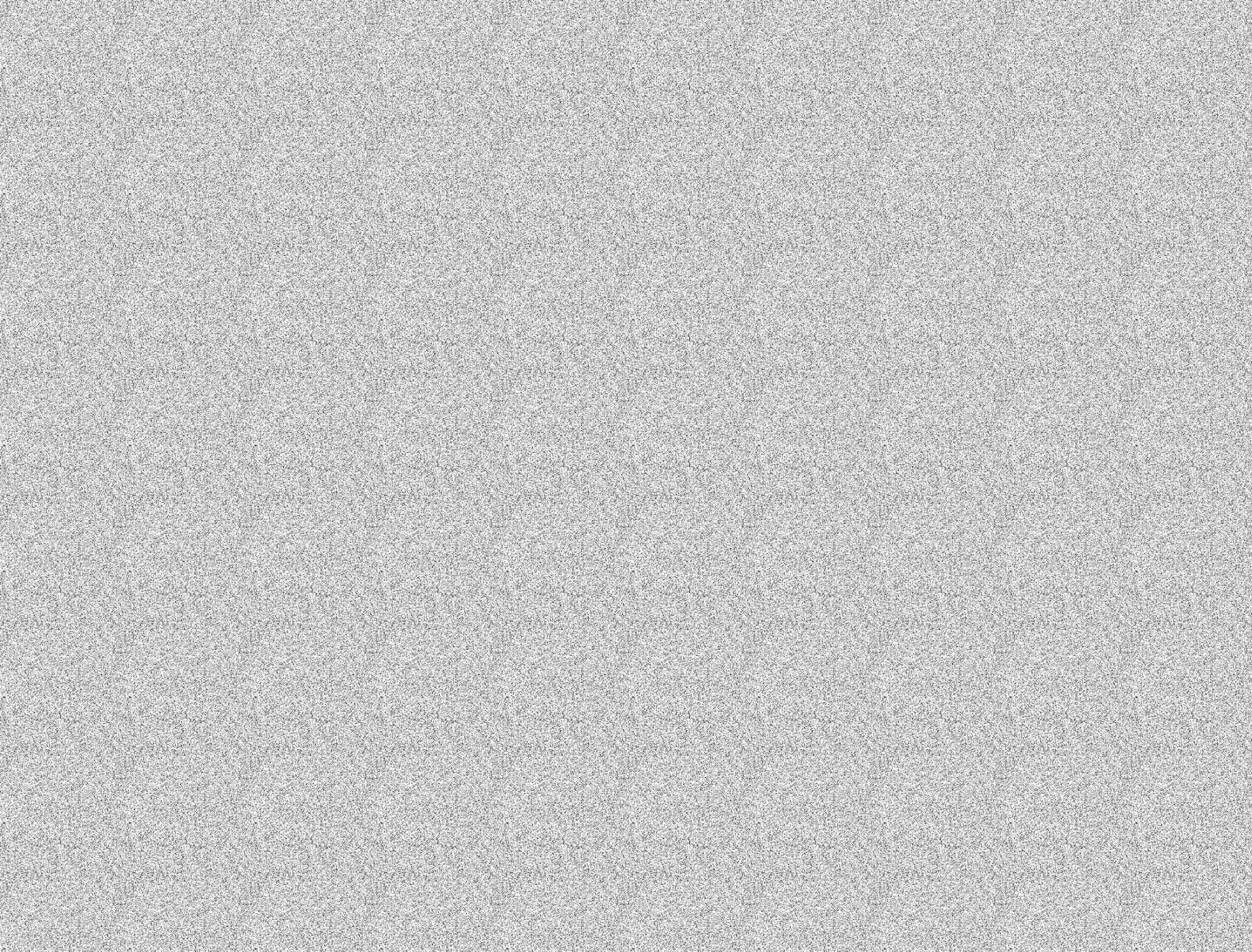
The Concept of End-to-End Integration
End-to-end integration refers to the alignment and continuous interconnection of all stages of a process, from inception to completion. In the context of materials development, it fosters a symbiotic relationship between research and production. It transcends traditional barriers, creating a coherent workflow that enables materials providers, factories, and manufacturers to collaborate effectively.
Traditional models often suffer from fragmented processes, disjointed communication, and a lack of real-time information flow. These disconnects lead to inefficiencies, prolonged development cycles, and inconsistencies in product quality.
MaterialsZone's platform is designed to bridge the gap between research and production. It integrates various stages of development, supporting quick and safe scale-up, thus exemplifying the true essence of materials informatics.
The platform's ability to aid in raw material substitution without compromising quality is a testament to its innovative design. It ensures that product specifications are met even when alterations are made to the raw materials used, epitomizing efficiency in materials data management.
Advantages of End-to-End Integration
One of the most significant advantages of end-to-end integration is the acceleration of R&D cycles. By eliminating prolonged trial and error, Materials Zone's platform offers up to 90% savings in time to market, thus aligning with modern demands for rapid commercialization.
The analytical use of data-driven strategies curtails production mishaps. It streamlines the production process, ensuring efficiency and cost-effectiveness, marking a vital step towards minimizing the traditional challenges faced in materials development.
Real-world Applications of End-to-End Integration
Various industries have adopted end-to-end integration, resulting in enhanced collaboration and efficient production. Specific case studies reveal the practical benefits and the transformative impact of this approach.
MaterialsZone's platform has been instrumental in implementing end-to-end integration in different industrial scenarios. These success stories demonstrate the platform's effectiveness in bridging research and production, enhancing materials data management, and facilitating materials informatics.
Future Prospects and Technological Developments
The integration of AI and ML in end-to-end integration heralds an exciting phase in materials development. These emerging trends highlight the evolution of materials informatics, pushing the boundaries of what is achievable.
Like any evolving technology, end-to-end integration faces challenges, including adaptability, scalability, and security. However, with strategic planning and execution, these challenges can be overcome.
Conclusion
End-to-end integration is central to the future of materials development. By bridging research and production, MaterialsZone is fostering a new paradigm in materials data management and materials informatics.
The platform's ability to transform traditional processes into a coherent and streamlined workflow position it at the forefront of this evolving field.
As a holistic solution, MaterialsZone's offerings hold profound implications for scientists, researchers, and industry leaders seeking to innovate and excel in the modern materials science landscape.