7 Must-Have Elements for a Great Validation Plan
When innovation moves faster than oversight, it's easy for critical validation steps to fall through the cracks. In regulated industries like pharma, food tech, chemicals, and advanced materials, that disconnect shows up in familiar ways: late-stage product delays, unclear audit trails, or gaps in process control that create compliance risk. A single failure rarely causes these issues. They often stem from missing or incomplete validation plans that can't keep pace with evolving systems and cross-functional teams.
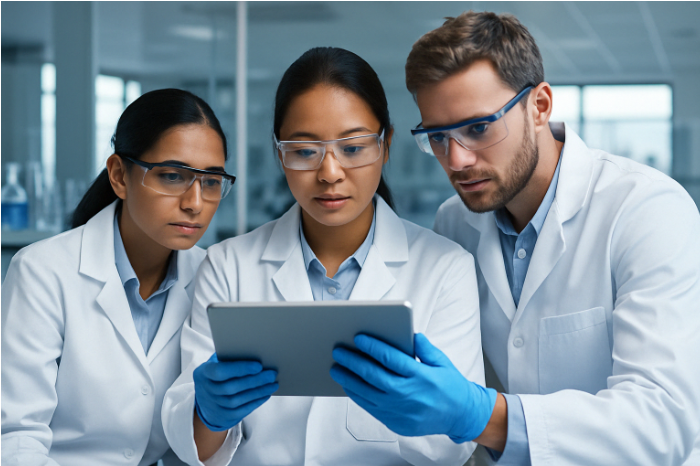
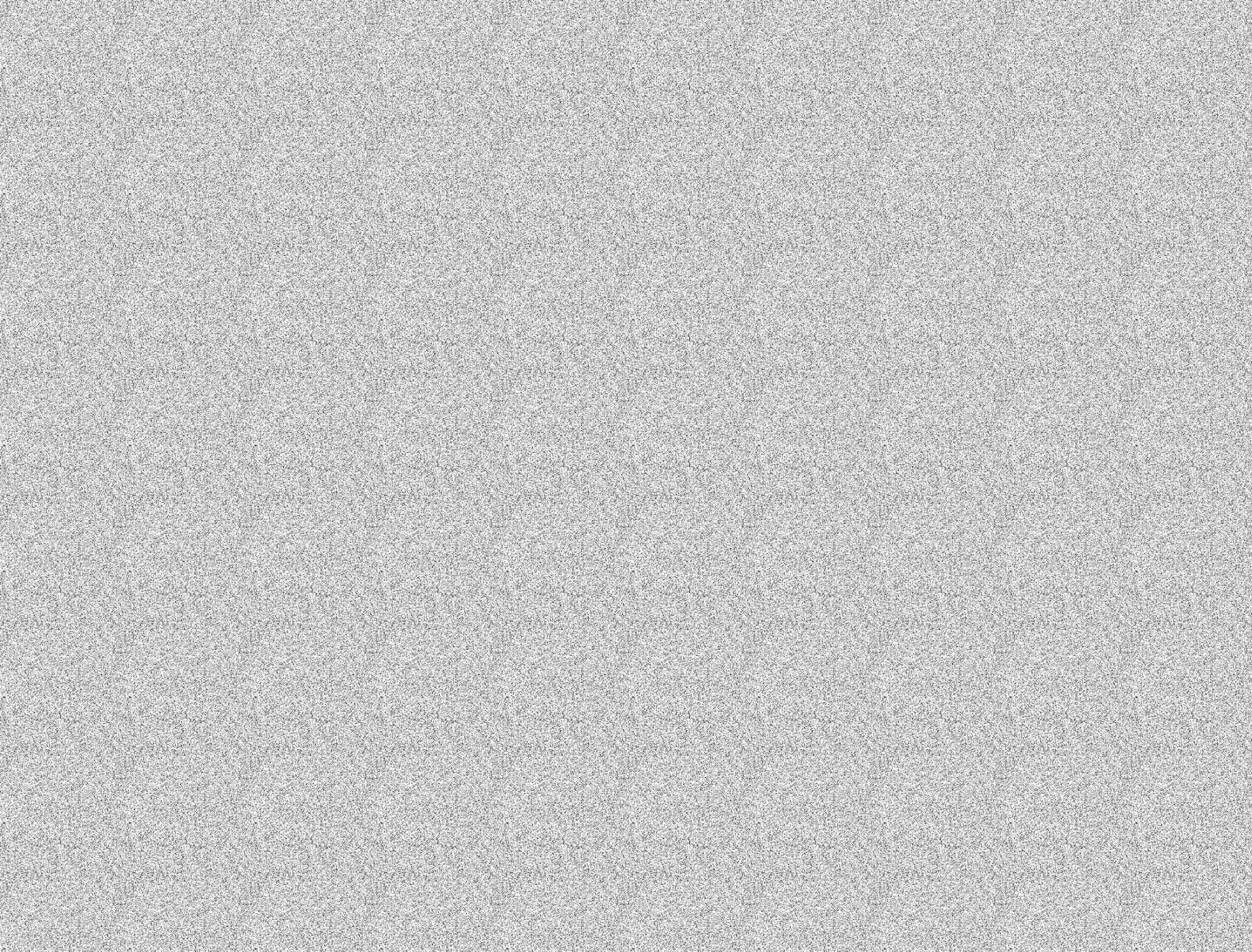
Inconsistent validation is becoming a major exposure point. As systems grow more complex and teams work across disciplines, maintaining control and compliance has become harder to manage. Recent research shows that 46% of professionals across quality, validation, and manufacturing functions expect a need for more agile and adaptable validation processes to respond to changing regulations and technologies. This trend highlights the growing recognition that rigid or outdated approaches are no longer sufficient for modern R&D environments.
To meet that bar, teams need more than reactive paperwork or fragmented protocols. A clear validation plan provides structure from the start by defining what needs to be tested, how it will be evaluated, and which standards apply. Let’s explore the essential elements that make up a great validation plan.
What Is a Validation Plan, and Why It Matters in R&D
In regulated environments, validation refers to the documented process of confirming that a system, method, or process consistently performs according to predefined requirements. It's a core quality assurance activity that helps ensure reliability, safety, and compliance across production and R&D workflows.
A validation plan is a formal document outlining how this will be achieved. It defines the scope of validation activities, the criteria for success, and the responsibilities of involved teams. A validation plan ensures that critical systems—whether physical equipment, digital tools, or laboratory procedures—are tested, reviewed, and documented in a consistent, auditable way.
The purpose of a validation plan is twofold:
- To provide a clear execution framework that defines what will be tested, how success will be measured, and who is responsible at each stage.
- To ensure traceability by documenting each phase in a way that supports audits, enables team visibility, and meets regulatory expectations.
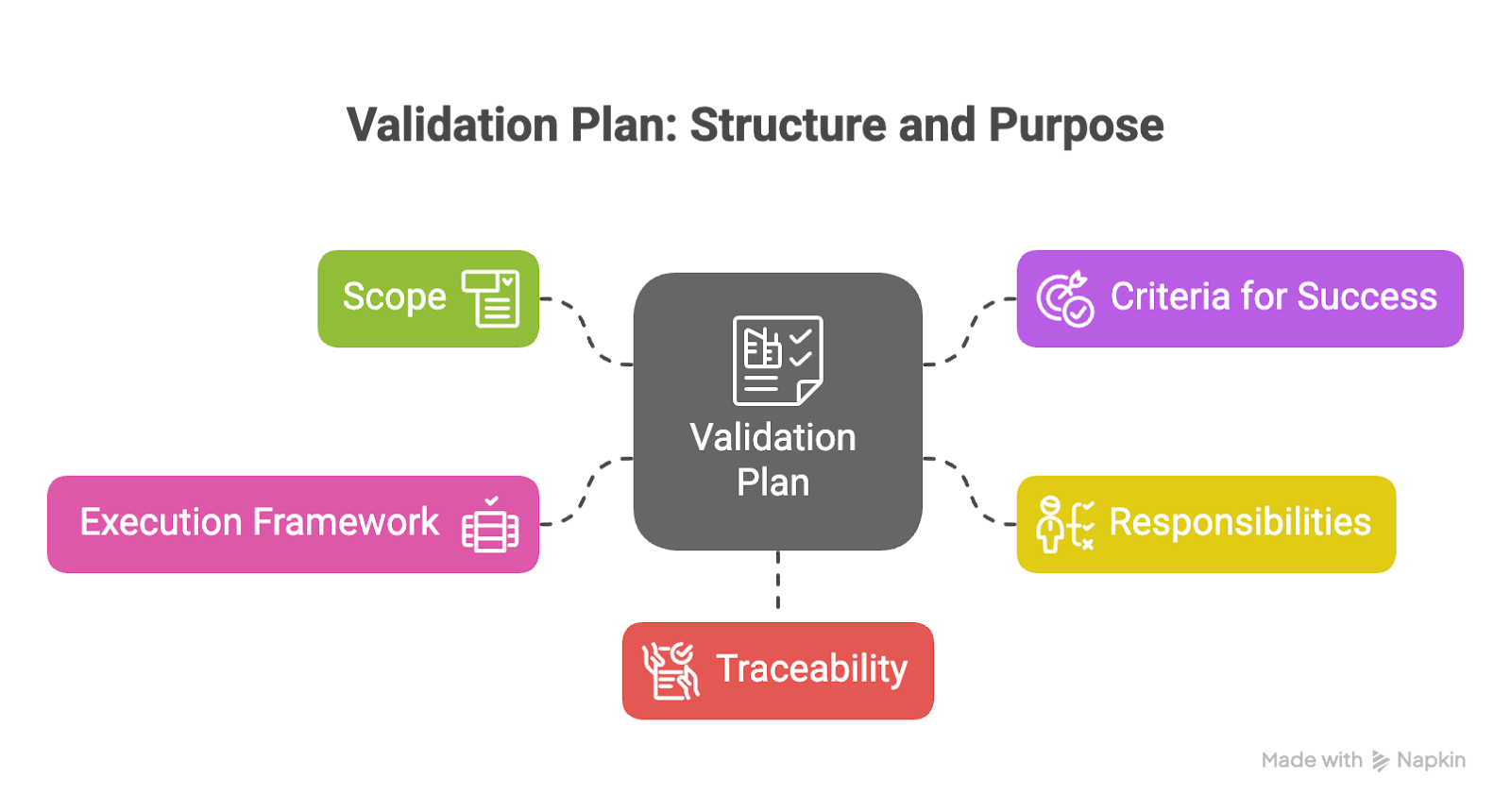
Validation plans are used across multiple functions, including QA, IT, R&D, and production. A well-structured plan helps ensure that system changes are introduced safely and predictably, reduces the risk of compliance issues, and enables teams to rely on the tools that support product development.
Types of Validation Plans
Validation plans must be tailored to reflect the specific systems, risks, and compliance requirements within your operation. Depending on how your organization manages data, equipment, and processes, you may need one or more types of validation, each focused on a different aspect of control. Here are the most common types of plans:
Process Validation Plan
Process validation plans define how a production process will consistently yield outputs that meet established quality specifications. These plans are essential in Good Manufacturing Practice (GMP) environments and typically include protocol design, data collection, and clear criteria for demonstrating reproducibility.
Equipment Validation Plan
These plans focus on ensuring that manufacturing or laboratory equipment performs reliably under expected conditions. They typically involve installation qualification (IQ), operational qualification (OQ), and performance qualification (PQ), all of which confirm that equipment functions as intended in its production environment.
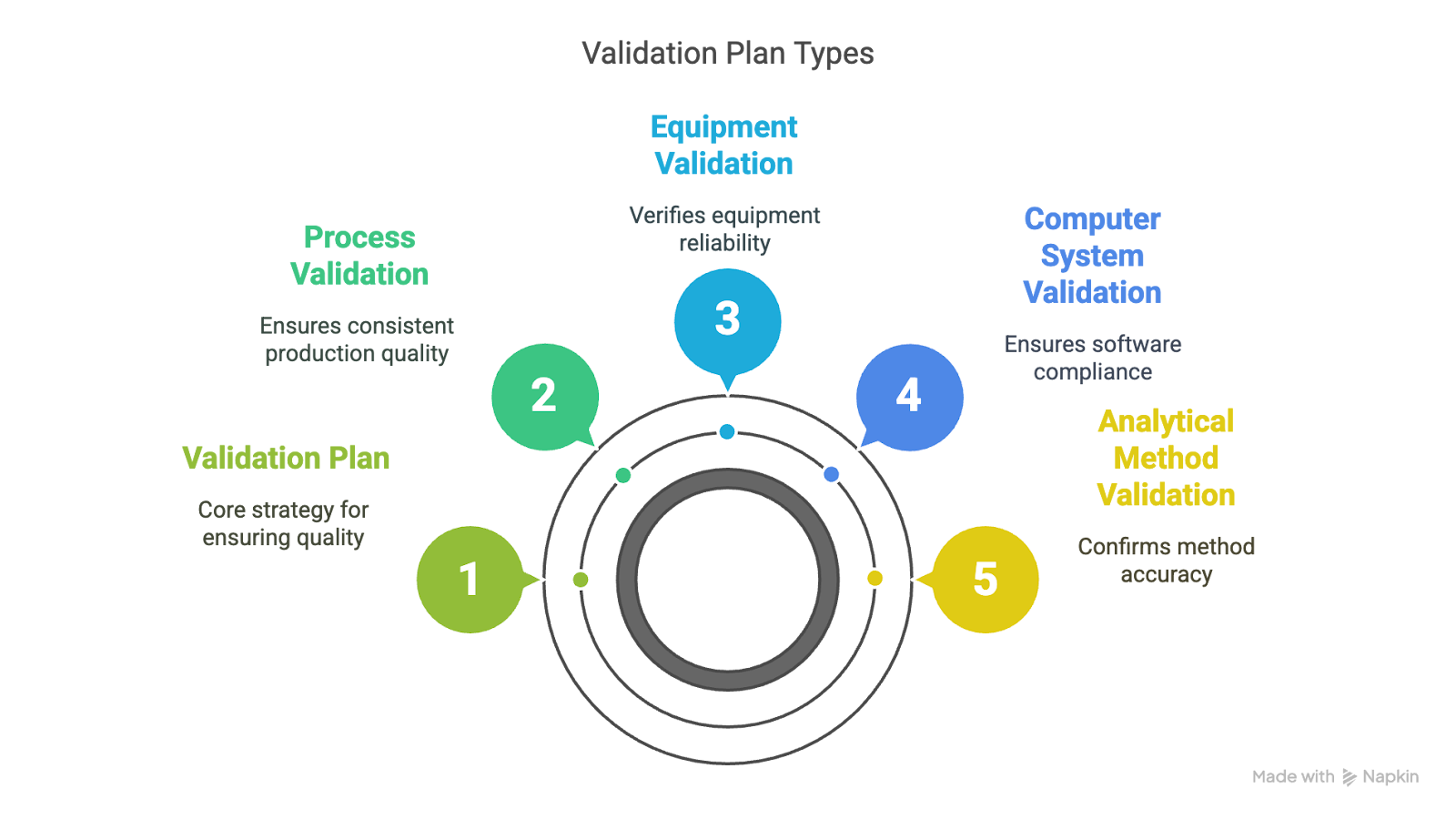
Computer System Validation (CSV)
CSV plans apply to software systems such as electronic lab notebooks (ELNs), laboratory information management systems (LIMS), and enterprise resource planning (ERP) platforms. These plans are essential for GMP compliance and must address requirements like 21 CFR Part 11, which governs electronic records and signatures.
Analytical Method Validation Plan
Commonly used in laboratory settings, these plans verify that a testing method is accurate, reproducible, and fit for its intended use. They typically assess parameters such as specificity, precision, linearity, and robustness, particularly when methods are applied to batch release or stability testing.
Cleaning Validation Plan
Cleaning validation ensures that cleaning procedures effectively prevent contamination between product runs. These plans are vital in pharmaceuticals and food production, where residual products or cleaning agents must be reduced to acceptable levels before switching to a new batch or product.
5 Benefits of a Great Validation Plan
A well-executed validation plan strengthens day-to-day operations and sets teams up for long-term success. Here's what it helps organizations achieve:
1. Boosts Product Safety & Reliability
Validated systems are less likely to fail in production. A well-structured validation plan helps protect product integrity and minimize downstream risks by confirming that equipment, processes, and software perform as intended.
2. Reduces Project Delays
Clear test protocols, acceptance criteria, and role assignments prevent last-minute rework or failed validations that can delay product release or system deployment.
3. Ensures Audit Readiness & Documentation Compliance
When validation activities are consistently planned and documented, teams can provide required records on demand and demonstrate compliance during audits, without scrambling to patch missing information.
4. Improves Cross-team Communication
Validation plans bring QA, R&D, production, and IT into alignment by clearly defining who is responsible for each part of the process. This prevents miscommunication and ensures smoother execution.
5. Manages Risk Through Structure & Foresight
A well-scoped plan prioritizes high-risk systems and sets expectations for testing and documentation. It reduces the likelihood of missed steps, audit findings, or overlooked compliance requirements.
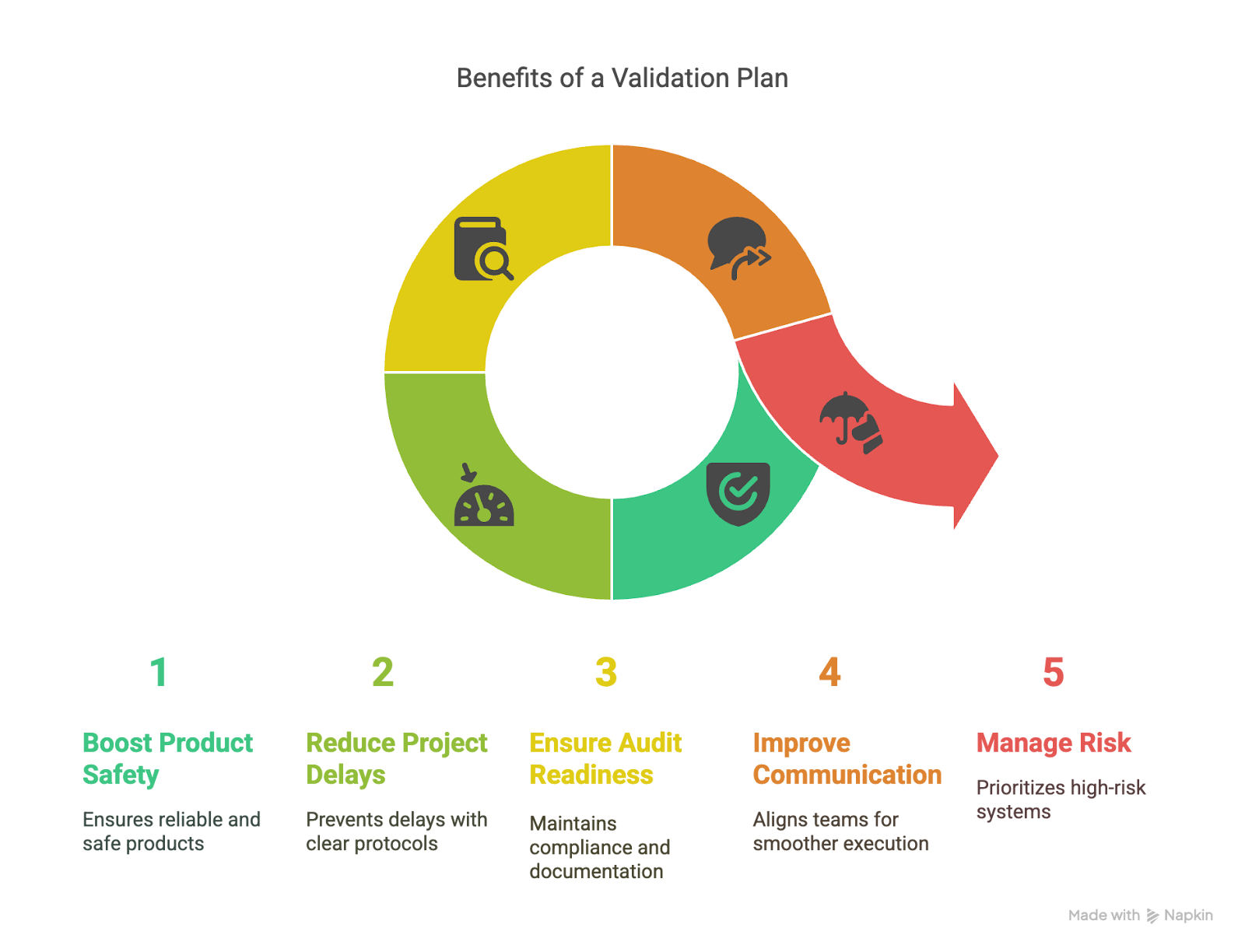
7 Elements to Include in a Great Validation Plan
1. Clear Validation Objectives
Every effective validation plan begins with a clear definition of purpose. This section should specify what is being validated, the reason for the validation, and the criteria that define success. A well-written objective aligns QA, R&D, IT, and any external partners on the scope and expectations from the outset.
Example objectives might include:
- "Validate XYZ software platform for compliance with 21 CFR Part 11."
- "Ensure that automated cleaning procedures meet GMP standards to prevent allergen cross-contamination."
Objectives should be concise but meaningful. Reference the system or process name, the regulatory driver, and the intended outcome. This specificity provides immediate clarity and prevents scope creep later in the project.
2. Defined Roles and Responsibilities
Validation efforts can easily stall when it's unclear who's responsible for what. A solid plan should clearly assign roles for each phase, such as writing protocols, executing tests, reviewing outcomes, and approving documents. When responsibilities are vague, handoffs get missed, and accountability breaks down.
These roles can be mapped using a RACI matrix (which identifies who is responsible, accountable, consultable, and informed for each task) or a simpler ownership table that lists each person or team next to their assigned activity. External vendors involved in equipment delivery or system qualification should be included here, too.
Tools like MaterialsZone's Collaboration Hub help teams formalize these assignments and track them in real-time so QA, IT, R&D, and others stay aligned without relying on disconnected documents or email threads.
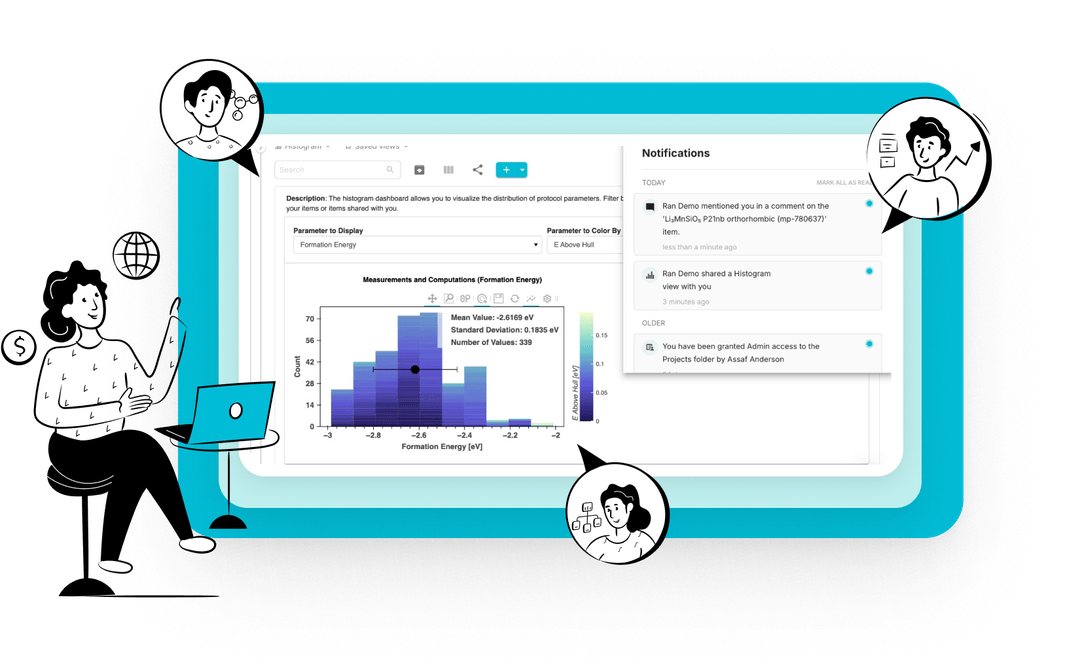
3. Risk Assessment Strategy
Not every system carries the same level of risk, and your validation plan should reflect that. A risk-based approach ensures you focus resources where they matter most, which is systems that affect product quality, patient safety, or even regulatory compliance.
- Start by defining how you'll evaluate risk. A standard method is to assess the potential severity of failure, how likely it is to occur, and how easily it could go undetected.
- Based on those criteria, systems can be categorized accordingly. For example, a viscometer used for final product testing would be considered high-risk and require complete validation protocols. By contrast, a non-GMP tool like HR software may only need basic documentation.
This strategy aligns with guidance from ICH Q9, which encourages structured risk management in regulated environments. Specialized software can help teams apply this strategy by linking validation scope to system risk and managing the level of documentation required for each category.
4. Detailed Validation Deliverables
A well-documented validation effort depends on clearly defined and properly stored deliverables. These documents create the audit trail that shows systems were tested, reviewed, and approved in line with internal protocols and regulatory standards.
Typical deliverables include:
- The validation plan itself
- User and functional requirements (URS and FRS)
- Qualification protocols, including installation, operational, and performance qualification
- Test scripts and data records
- A final validation summary report that confirms all steps were completed and all criteria were met.
The plan should also define how documents will be version-controlled, reviewed, and stored. Without a clear process, teams risk using outdated files or losing traceability during audits or re-validations. Platforms like MaterialsZone make it easier to manage validation documentation by centralizing records, automating version control, and ensuring traceability during audits.
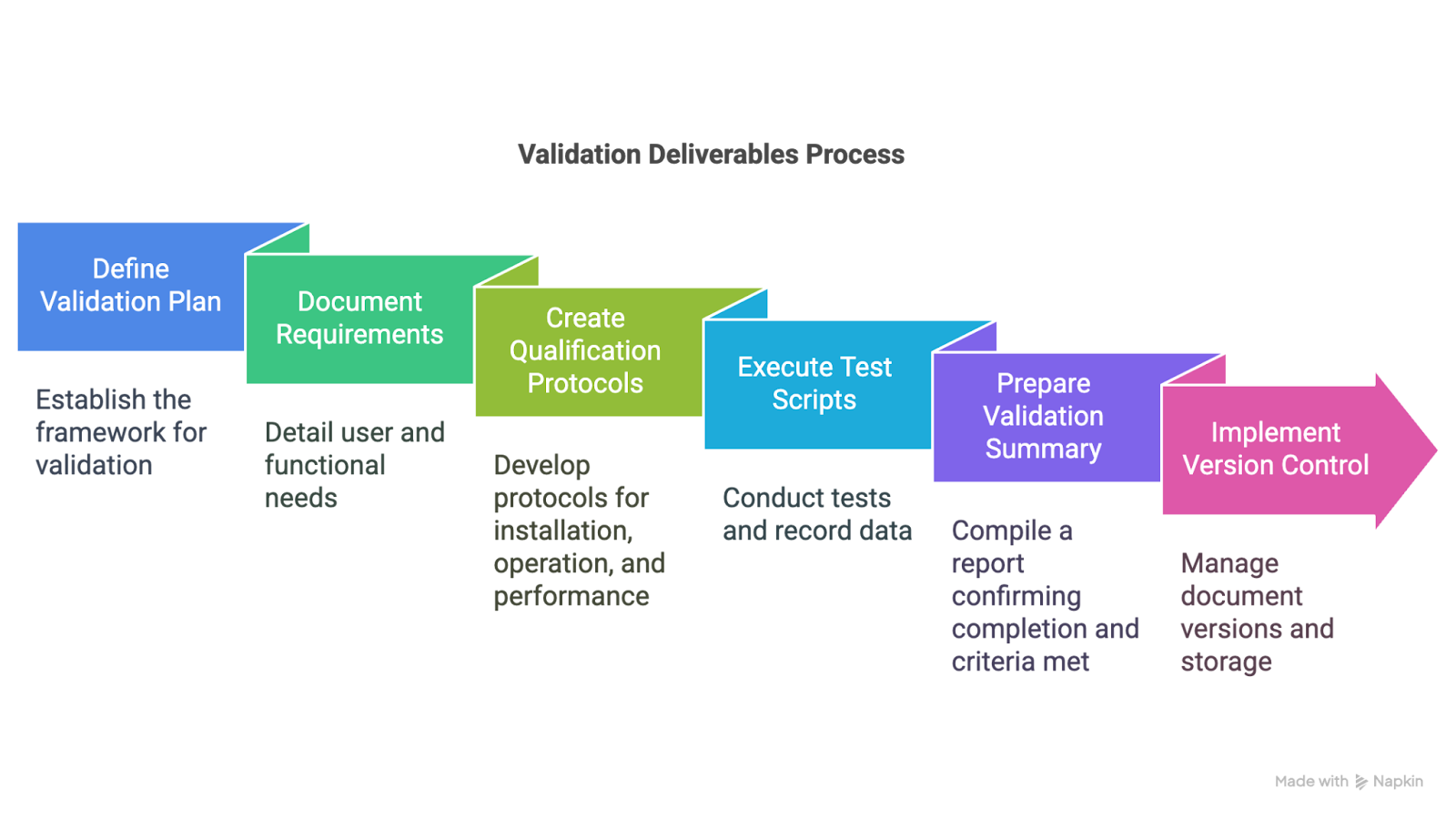
5. Acceptance Criteria and Test Plans
Test plans must be built around objective, measurable criteria. Vague pass/fail language introduces unnecessary risk. For each validation activity, define exactly what constitutes success, how results will be measured, and who is responsible for reviewing and approving outcomes.
Examples of clear criteria might include:
- “The temperature remains within ±0.5°C for a continuous 24-hour run.”
- “An audit trail is retained and accessible for a minimum of 24 months.”
The plan should also describe how deviations are logged, investigated, and resolved. It should specify who is authorized to approve retests or override results, and under what conditions those actions are permitted. Clear test documentation supports consistency and ensures your results are defensible during audits or inspections.
6. Change Control and Deviation Management
Any change to a validated system—whether hardware, software, methods, or processes—must be formally assessed, documented, and approved before implementation. Without a clear process, even minor updates can pose compliance risks or compromise prior validation efforts.
- Your plan should outline how changes are evaluated for impact, who reviews them, and how final approval is granted.
- It should also define how deviations are logged, how root causes are investigated, and how corrective and preventive actions (CAPAs) are implemented when needed.
Advanced material informatics platforms support these practices by capturing changes and deviations automatically through its validation workflows. This data capture helps teams maintain full traceability while meeting internal and regulatory requirements.
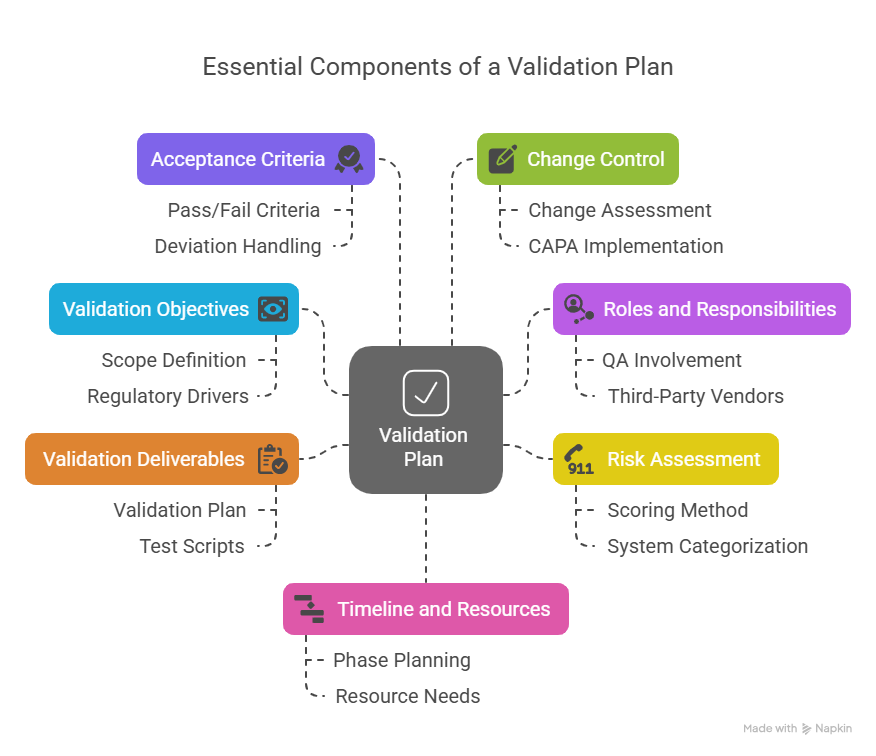
7. Timeline and Resource Planning
Many validation efforts fail not because of poor execution, but because of unrealistic timelines and missing resources. A well-built validation plan should account for how long each activity will take, who needs to be involved, and what tools or environments are required at each stage.
Include a phased schedule that outlines key milestones, such as:
- Drafting and approving protocols
- Executing tests
- Reviewing results
- Final approvals and summary documentation
In parallel, list the resources needed to complete each phase. These could include validation engineers, QA reviewers, IT or lab support, software and demo platforms, instruments, or lab space. Resource bottlenecks such as limited availability of qualified personnel or shared equipment should be identified early.
Contingency planning is also essential. Build in time for potential retests, delayed approvals, or scope changes. If your validation is linked to a more significant milestone, like a product release or regulatory submission, your timeline should clearly show how validation activities align with those deadlines to prevent critical path delays.
Plan Smarter and Validate with Confidence
A robust validation plan is one of the most effective tools teams have to reduce risk and maintain control in regulated environments. When validation is approached methodically and supported by clear roles, realistic timelines, and risk-based thinking, it strengthens compliance and improves day-to-day execution.
MaterialsZone’s platform brings speed and structure to that process. It enables data-driven validation with centralized documentation, automated tracking, and analytics that make oversight easier and more transparent. Teams can move faster without compromising traceability or regulatory readiness.
Ready to build smarter validation plans with less manual overhead? Book a demo to see how MaterialsZone streamlines validation for R&D-intensive, regulated environments.