New Product Introduction (NPI): The Essential Guide to Getting it Right
Bringing a new product to market in regulated, materials-intensive industries is one of the most demanding stages of innovation. The challenge often isn’t the idea itself, but its execution. What it comes down to is whether the formulation developed in the lab can be validated, documented, and transferred into production without friction. When that process breaks down, promising innovations lose momentum before reaching commercial scale.

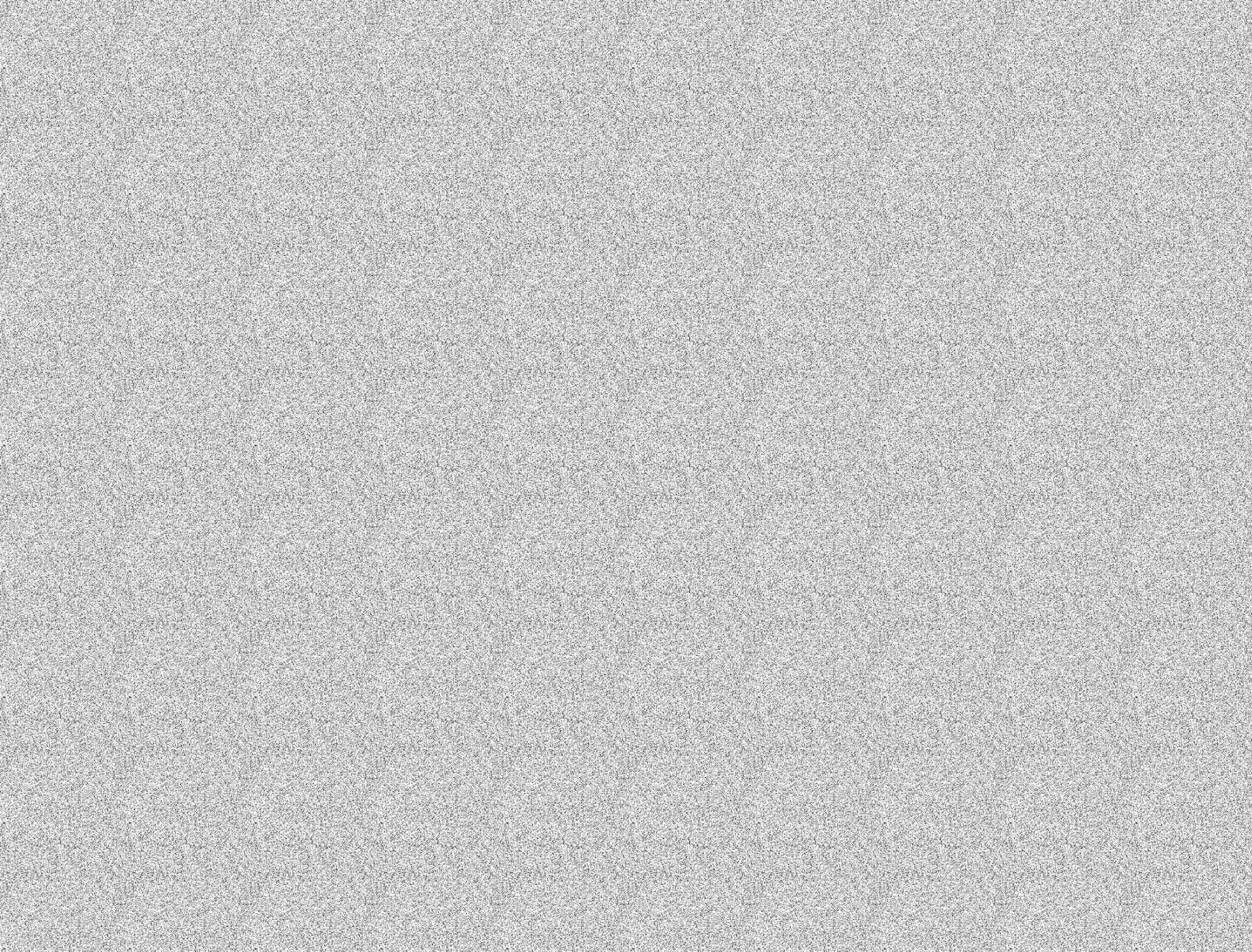
New Product Introduction (NPI): The Essential Guide to Getting it RightResearch shows that 95% of product launches fail to meet expectations. In sectors like pharmaceuticals, chemicals, food and beverage, and advanced materials, these failures are frequently linked to incomplete lab documentation, validation gaps, or poor transfer to manufacturing. A structured New Product Introduction (NPI) process addresses these risks by creating a reliable path from early development to launch, with compliance, traceability, and reproducibility built in.
NPI begins where most issues arise—in the lab. It brings structure to experimental workflows and aligns early decisions with downstream requirements to ensure that products are built for scale from the start. Let’s take a closer look at the new product introduction process and how to implement it successfully.
What is New Product Introduction (NPI)?
New product introduction (NPI) is a structured, multi-phase process that carries a product from initial concept through prototyping, validation, manufacturing, and launch. It begins in R&D, where lab work is documented in detail, and adds clear checkpoints and decision gates as the product advances toward production.
The NPI process is designed to improve product quality, streamline production, manage risks, reduce waste, accelerate time to market, and cut costs by applying practical insights gained from past development efforts.

NPI supports teams that operate in technically demanding, compliance-driven environments:
- R&D leaders use it to capture experimental data in a consistent, searchable format.
- Innovation managers rely on it to keep feasibility studies aligned with market requirements and business goals.
- QA and validation specialists depend on its audit-ready records to demonstrate that every test meets regulatory standards.
- IT and data professionals maintain the shared systems that connect laboratory results to downstream execution.
By providing standardized procedures, full version history, and early validation, NPI gives organizations confidence that a formulation proven in the lab will perform the same way on the production line. Turning scattered lab notes into a single, traceable record builds the foundation needed to scale new products without costly surprises later in development.
Benefits of New Product Introduction (NPI)
The new product introduction process offers several advantages to regulated, materials-intensive organizations, including:
Fewer Handoff Failures Between Lab and Production
NPI converts raw lab work into a single, structured record that includes the full recipe and the approved process parameters. Production engineers no longer rely on informal notes or hallway conversations, so the transition from bench-scale to pilot line stays on plan.
Faster Time to Market
Each phase of NPI comes with defined entry and exit criteria. When a task falls behind, the delay is visible early, which gives leaders time to fix problems before they cascade into the launch schedule.
Standardized Lab Procedures and Documentation
NPI establishes uniform lab procedures upfront and records every step in version-controlled files. Because each experiment follows the same instructions for materials and equipment settings, teams can reproduce results on demand while auditors trace any adjustment quickly.
Integrated Compliance & Validation Checkpoints
Regulatory evidence is gathered inside the same workflow that drives technical tasks. As soon as a validation test finishes, its results are logged with the correct approvals, so nothing has to be recreated on the eve of an inspection.
Clearer Decisions Based on Real Data
All experimental outputs flow into a shared database. Decision-makers can review live performance metrics alongside historical change logs and make go-or-no-go calls with confidence.

6 Steps to Implement New Product Introduction Successfully
A disciplined new product introduction framework turns early-stage ideas into commercial products without the late-cycle surprises that drain budgets and derail schedules. These six steps give R&D and innovation leaders a practical path to set up or refine the NPI process:
Step 1: Identify and Define the Opportunity
Every successful NPI process begins with a clearly scoped opportunity. At this stage, R&D and innovation teams assess whether a product idea addresses a real market need and whether the lab is equipped to develop a viable formulation.
Early validation helps prioritize feasible concepts, align internal resources, and plan development activities with fewer downstream adjustments. It ensures teams invest in ideas with a clear technical and commercial path from the outset.
How to do it:
- Use this structured framework to evaluate feasibility:
- Gathering internal lab data.
- Understanding customer pain points.
- Studying market trends.
- Assessing material availability.
- Next, conduct mini-experiments to test key assumptions about the product.
- Use an advanced materials informatics platform to aggregate prior experimental data and outcomes, and help your teams avoid redundant efforts. You can search for similar past formulations and understand which approaches delivered viable results.
Step 2: Design and Develop the Prototype
With feasibility confirmed, the next step is to build a prototype—a controlled, testable version of the product developed under defined lab conditions. This is where early concepts translate into experimental procedures that can be repeated and measured. A well-structured prototype provides the baseline needed for validation, scale-up, and eventual production transfer.
To serve its purpose, the prototype must be developed using standardized lab procedures and complete version control. Each run should be documented in detail, allowing teams to isolate performance variables and trace changes over time.
How to do it:
- Establish a standardized protocol for lab procedures, including:
- Document raw material grades and sources.
- Define equipment parameters and environmental conditions.
- Set measurement and test intervals.
- Log each trial using consistent formats.
- Include failed runs, photos, annotations, and timestamps in the documentation for each prototype run to capture the full experimental context.
- Use MaterialsZone to version each prototype automatically, track procedural changes over time, and find links between specific variations and performance results. The platform ensures every trial is traceable and reproducible, making it easier to move forward with confidence.

Step 3: Validate Against Functional & Regulatory Requirements
Once a prototype is in place, it must be validated to confirm that it performs as expected and complies with relevant standards. The validation includes both internal functional benchmarks and external regulatory requirements tied to safety, quality, or industry-specific protocols. At this stage, the goal is to demonstrate that the product is stable, repeatable, and ready to move forward without introducing risk.
A clear validation plan helps teams define what success looks like before testing begins. This level of structure is essential in regulated environments where products are subject to strict criteria and must pass formal inspections before release. Thorough, well-executed validation reduces the risk of compliance gaps, rework, and delays—and ensures every result is backed by traceable data.
How to do it:
- Develop a validation plan that defines the required performance metrics for each key attribute. Align each protocol with product specifications and regulatory expectations from the start.
- Standardize how validation tests are performed to ensure repeatability. Where needed, test under varied lab conditions to verify consistent results.
- Assign a clear owner to each validation task. Include specific checkpoints for data review and sign-off to maintain traceability.
- Log all test data, version each dataset, and link outcomes directly to their corresponding criteria in a materials informatics platform. It ensures audit readiness and reduces preparation time when results need reviewing.
Step 4: Prepare for Scale-Up and Production Transfer
This step ensures that lab-developed work can be executed accurately and consistently in a manufacturing environment. It marks the transition from experimentation to operational readiness, so process details and material specifications must be clear, controlled, and production-ready.
Many new product introduction efforts stall here because lab procedures aren’t documented in a way that production teams can apply without confusion or delay. To enable a smooth transfer, all technical elements must be finalized and approved for use outside the lab, including the validated formulation, process parameters, test methods, and inspection limits.
How to do it:
- Finalize the bill of materials, equipment settings, and test methods that were confirmed during validation. Check that each item reflects the approved version.
- Convert specifications into a format that production can implement directly. Avoid handoffs that require interpretation or restatement.
- Consider using a guided demo to walk teams through the transfer.
- Package all production-ready documentation into a centralized, controlled format that includes necessary safety information and procedural requirements.
- Employ a platform like MaterialsZone to generate structured, version-controlled outputs based on validated lab data. These outputs, such as finalized process parameters and formatted specifications, can be transferred directly into production workflows to reduce miscommunication and ensure traceability across teams.

Step 5: Launch the Product
Launch marks the point where a validated product moves from preparation to market release. This phase brings together the finalized technical documentation, required regulatory approvals, and any production or quality protocols that must be in place.
A well-executed launch ensures that every team involved, including QA, regulatory, supply chain, and commercial groups, has what they need to support a controlled and compliant release.
When structured properly, the launch phase reduces the risk of avoidable delays and helps prevent execution errors that could impact performance or compromise regulatory status. It also ensures that all teams stay aligned around a single, verified plan of record.
How to do it:
- Build a launch readiness checklist that covers documentation status, regulatory clearance, QA approvals, and stakeholder sign-offs.
- Confirm that each functional group has completed its responsibilities and has access to the latest approved product information.
- Consider a soft launch or pilot run to validate readiness in a controlled setting before full-scale release.
- A materials informatics solution can provide visibility into critical readiness indicators across validation, documentation, and procedural control. It helps teams stay aligned and create a consistent product experience required to support product-led growth strategies after launch.
Step 6: Monitor, Analyze, and Iterate Post-Launch
The final step of new product introduction ensures that product performance in the field is captured, analyzed, and used to inform future development. Once a product is released, usage conditions can reveal issues that were not detectable during lab testing. These signals must be recorded and linked to the original experimental work.
Post-launch monitoring is critical in regulated or high-risk environments, where unresolved issues can lead to compliance failures or degraded product performance over time. It also supports long-term innovation by grounding future improvements in observed results rather than assumptions.
How to do it:
- Build workflows for collecting product data after release, including lot-level performance and reports from technical or customer-facing teams.
- Feed post-launch input into the same system used to manage lab results and validation history.
- A modern materials informatics platform can be used to link post-launch data to specific lab procedures and experiment history. This linkage creates a closed feedback loop supporting faster investigations and continuous improvement based on real-world performance.

Make NPI a Competitive Advantage from Lab to Launch
New product introduction creates a structured process that connects lab work to production. It helps teams move from early experimentation to launch by defining how procedures are validated, documented, and transferred. When the framework is in place, development moves faster and risks are addressed before they escalate.
MaterialsZone’s AI-powered materials informatics platform improves NPI by standardizing lab procedures and capturing experimental data in a structured format that’s ready for production use or regulatory review. It gives teams access to reliable, versioned results they can act on with clarity at the point of handoff. The result is an NPI process with a clear path from lab validation to production, where every step is grounded in traceable data and consistent execution.
Book a demo today to see how MaterialsZone can improve your new product introduction process.