Industries
Materials Science and Materials-Based Products consist of a diverse ecosystem of industries, including chemicals, advanced materials, fast-moving consumer goods (FMCG), pharma, and biotechnology, where companies innovate and manufacture essential products that form the backbone of modern infrastructure, consumer goods, healthcare, and technological advancements.
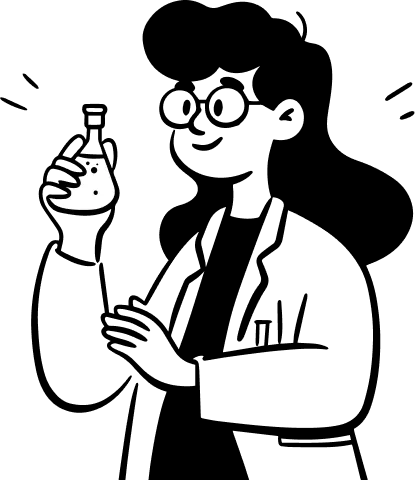
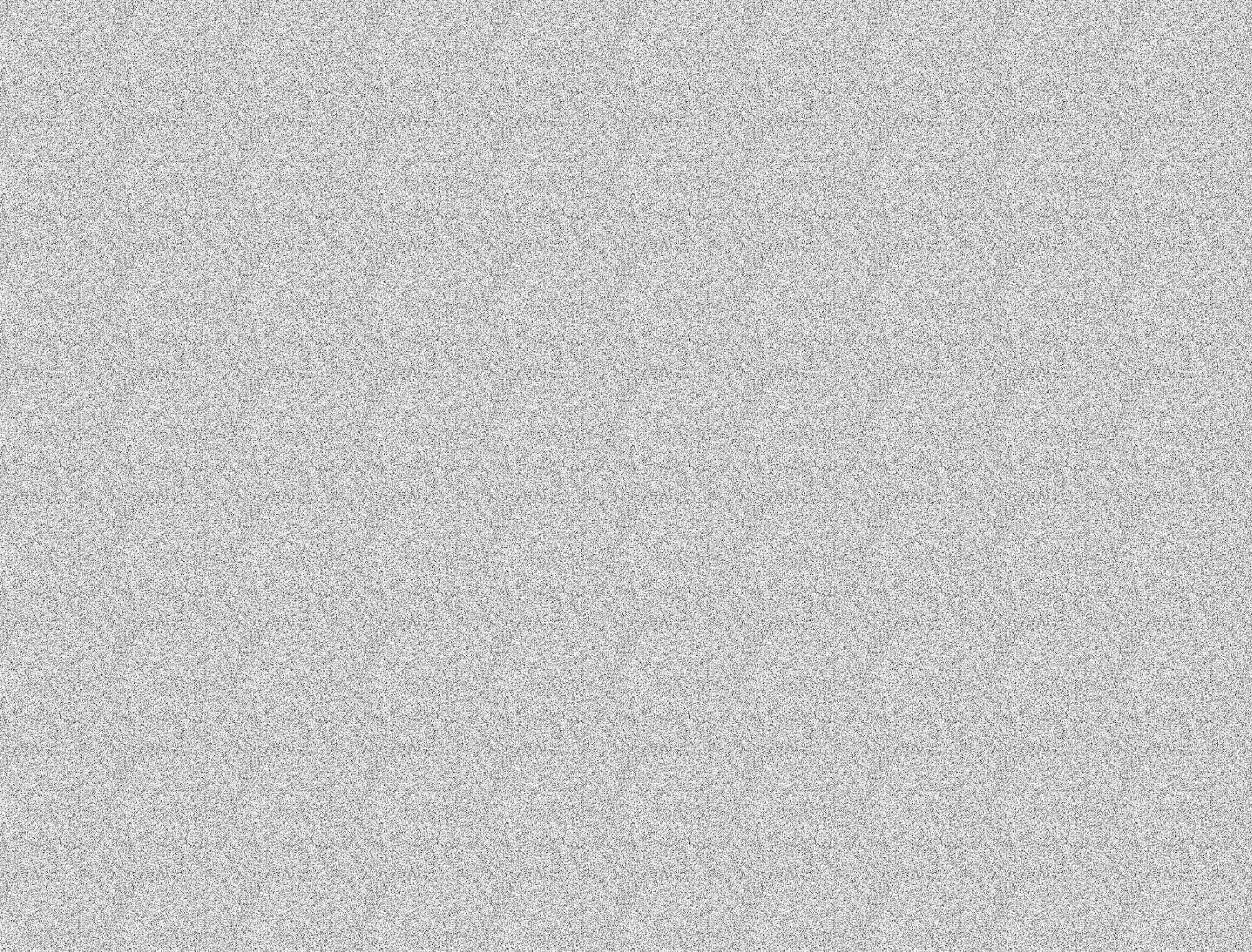
Chemicals
The Chemicals industry encompasses the production of essential substances like petrochemicals, industrial gases, polymers, and specialty chemicals, which are crucial in sectors ranging from agriculture and textiles to electronics and construction.
Advanced Materials
The Advanced Materials industry focuses on the development and production of high-performance materials such as composites, nanomaterials, batteries, and photovoltaics, this industry is key to innovations in energy, aerospace, electronics, and sustainable infrastructure.
Fast-Moving Consumer Goods
The FMCG industry involves the manufacturing and distribution of high-demand products with a quick turnover, such as food, beverages, personal care items, and household goods, which are essential to everyday consumer needs and are typically sold in large quantities at relatively low cost.
Come See What You Can Do With MaterialsZone
Schedule a demo with a materials expert today!
Request A Demo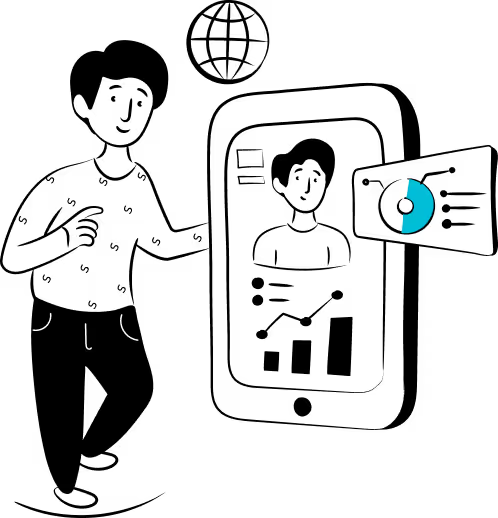